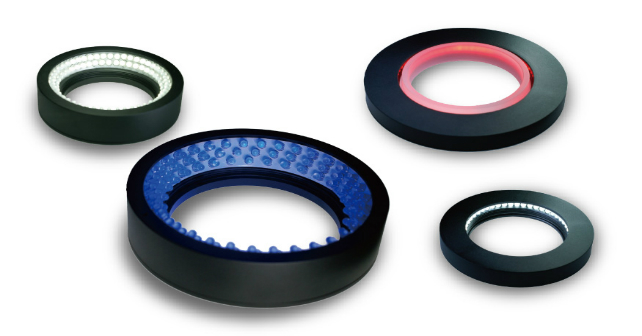
Even with the best will in the world, sometimes scratches and cracks can appear during the manufacturing of a product. Cracks are, of course, unacceptable, and products with them cannot leave the factory. Scratches, depending on the part or product, might be within tolerance. In both cases, catching the flaw early enough can mean that the part or product can be recycled.
Problem
With standard, integrated lighting the luminous radiance provided will not highlight a scratch or crack, but rather drown it in glare or shine. While such lighting might be sufficient for general shape detection, it is certainly not sophisticated enough to detect such a fine flaw like a scratch or a crack. Unfortunately that would make a camera miss a potential defect.
Solution
Highlighting fine features is the key, here, and the correct lighting solution can help your machine vision system to check the surface integrity of your product.
Ring LED lights: This type of lighting provides an even perimeter of light to the entire part under observations. It is particularly useful in situations like this when combined with low angle lighting.
Low Angle lighting: By mounting the light at a low angle the light is diffused and has the best chance of highlighting any potential flaws. An alternative solution, depending on surface type could be a diffusion dome.
Diffusion Dome: Creating an even, highly diffused lighting effect, increases the abilities of your machine vision to detect any surface flaws.
No Responses to “How to Set up Lighting for Detecting Scratches and Cracks”